Behind the scenes of the iGaming industry: how Amusnet is building its future
Friday 30 de August 2024 / 12:00
2 minutos de lectura
(Sofia).- We recently told you about the creation of the Type S line of land-based casino gaming machines that the company is developing. Today we ask what is behind their production and delivery, and the answers will be given by Kalin Pavlov, Manufacturing Manager at Amusnet.
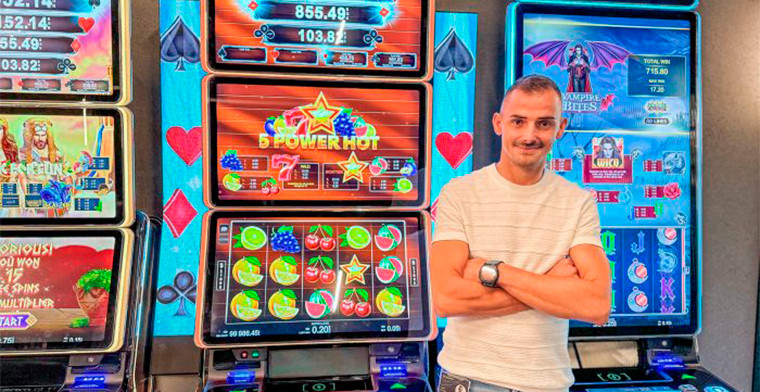
Kalin, what is it like to be responsible for the production of such an innovative product?
Creating our own series of slot cabinets is a natural extension of Amusnet's ambitious plans. Over the past 8 years, we have established ourselves as a reliable partner and producer of over 300 classic and modern casino games popular around the world. With cabinet manufacturing, we close the circle and cover almost all aspects of the industry, offering online casino, live casino and land-based solutions.
In an industry where every company strives to offer new and innovative products, this strategic decision gives us the opportunity to continue our development. In this case, the company also relies heavily on my experience of more than 12 years in the industry, going through all stages from technician to production manager at Amusnet. This allowed me to gain knowledge about the entire production cycle, which is still applicable today.
What are the steps before manufacturing a slot cabinet?
If I may joke with you and the readers, I would say that first of all, there should be orders and interest from casinos around the world and here. After the presentation of the cabinets at the largest exhibition in London in February, we too were surprised by the great interest and the number of orders that we expect to fulfill by mid-2025. The next step is to secure raw materials for production - a task that is not at all easy.
The components of the cabinets come from Bulgaria, Europe and China, and the body will be manufactured entirely in Bulgaria. Amusnet's strategic decision is to carry out all production in our factory in Sofia. This guarantees that each cabinet will meet our high quality standards. We believe that there are specialists with extensive experience in the country to help us in this endeavor.
One of the biggest challenges is choosing the right suppliers and partners, as well as the overall organization of the process. The key to good process planning turned out to be the integration of SAP as the main ERP solution to optimize the entire production. We are currently in the pre-production phase and are finalizing all the last details before the start of production of the first series machines, scheduled for October.
What is the biggest challenge you face in remote/home office work?
Staying focused and more distracted
Maintaining work-life balance
Effective communication with team members
Access to reliable technology and tools
A sense of isolation
What does Amusnet have in store for the rest of the year?
By the end of the year, we plan to produce 500-600 slot cabinets, and in 2025 we hope to increase production to 300 cabinets per month. Initially, the machines will be distributed in Bulgaria, Romania and Serbia, and from next year we expect them to reach countries in Africa, as well as those in North and South America.
New products appear every year and we have to keep up with customer trends and preferences. After the slot cabinets, we are planning the development of new terminals, roulette wheels and software. The Type S is just the beginning and we are ready to bring new and interesting offerings to the world stage.
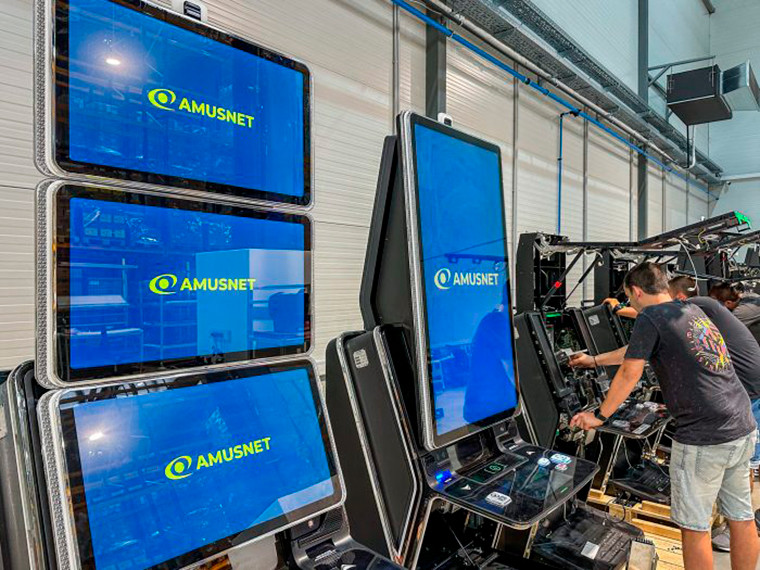
What is at the heart of the machine?
As we have mentioned, the parts for our machines come from many different countries, but the key element that makes a machine a reality is the team responsible for assembling it. Each part goes through quality control to ensure that it meets all requirements. The same process is repeated when the finished product is finished and ready to travel by water, land and air.
Imagine a puzzle with over 1000 pieces – that’s how many machines there are. Each part must be in the right place to get the expected result. All this happens on the assembly line, where colleagues check compliance with all standards and requirements.
The company’s goal is to create products with a distinctive style and innovative software and hardware, and to provide players with the best possible experience.
How will you maintain and service your slot cabinets?
After a machine is manufactured, maintenance and service follow. Typically, depending on the components, software and technologies built into it, each slot cabinet has a certain life cycle. For the hardware part, this period is about 10 years, and for the software part, about 5.
It is planned to create a technical center where customers will be able to turn to us in case of problems. It will operate 24 hours a day, 7 days a week, and in the future we plan to open local offices for the largest markets in which we operate. We expect the support team to reach 20 people next year and continue to grow.
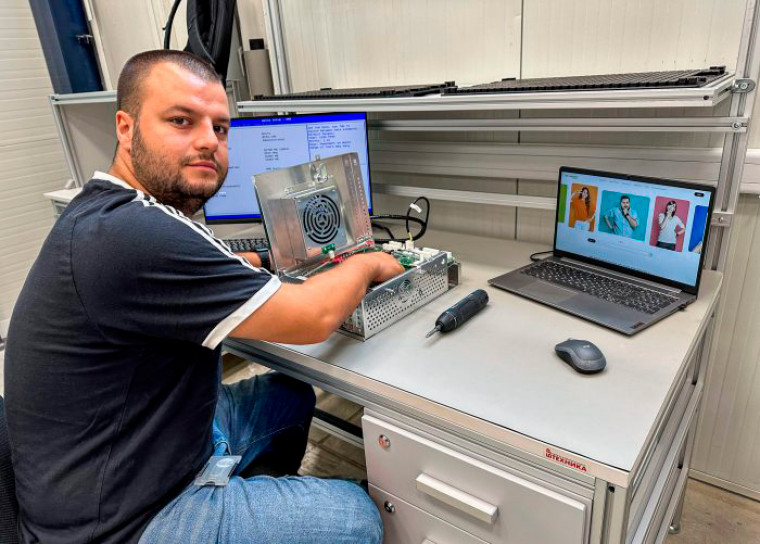
What knowledge and skills do people need to work in the team?
The work in our team is very specific and requires technical expertise as well as a strong desire for development. Every new employee undergoes extensive initial training, which is far from the standard you might imagine. From the beginning, newcomers are directly involved in working on the various machine components, gradually getting to know each of their parts and tackling increasingly complex tasks.
Experience with a variety of technologies and a desire for professional improvement are always considered an important asset. While there may be differences between industries, experience gained in other areas of manufacturing provides a solid foundation on which we can successfully build.
During the first days of work, colleagues get to know all the plans and components of the cabinets in detail. They learn everything they need to know, from the meaning of each screw to why the screens of some cabinets are curved. We strive to answer all questions related to the specifics of the work and the expectations of new colleagues who start working for us in production.
Everyone is encouraged to offer ideas to optimize the production process. Listening to the experiences of our employees and learning from each other is key for Amusnet.
Categoría:Analysis
Tags: AMUSNET,
País: Bulgaria
Región: EMEA
Event
Peru Gaming Show 2025
18 de June 2025
Facephi presented its digital identity verification solutions for the online gaming sector in Peru at PGS 2025
(Lima, SoloAzar Exclusive).- Facephi is consolidating its position as a strategic partner for responsible online gaming in Peru, presenting advanced identity verification, fraud prevention, and regulatory compliance solutions at PGS 2025, adapted to an increasingly digital and demanding ecosystem. In this interview, Bruno Rafael Rivadeneyra Sánchez, the firm's Identity Solutions Senior Manager, explores how its technology is redefining gaming security standards, with a preventative, seamless, and 100% regional approach.
Friday 18 Jul 2025 / 12:00
From PGS 2025, Win Systems Redoubles its Commitment to Peru: Innovation, Proximity, and Regional Expansion
(Lima, SoloAzar Exclusive).- In a revealing interview, Galy Olazo, Country Manager of Win Systems in Peru, analyzes the company's strategic role in one of the most thriving markets in the region. Its participation in the PGS 2025 trade show not only left its mark with its technological advances, such as the new Gold Club Colors electronic roulette wheels and the WIGOS management system, but also reaffirmed its commitment to the transformation of the sector and its consolidation in Latin America.
Tuesday 15 Jul 2025 / 12:00
Key debate during PGS 2025: Enforcement: Process to ensure compliance (laws, norms, rules)
(Lima, SoloAzar Exclusive).- During the 2025 edition of the Peru Gaming Show, the conference ‘Enforcement: Process to ensure compliance (laws, norms, rules)’ took place, with an international panel of professionals who debated about the current challenges to combat illegal gaming and guarantee the application of the laws in the sector, both in Peru and in the Latam region.
Monday 14 Jul 2025 / 12:00
SUSCRIBIRSE
Para suscribirse a nuestro newsletter, complete sus datos
Reciba todo el contenido más reciente en su correo electrónico varias veces al mes.